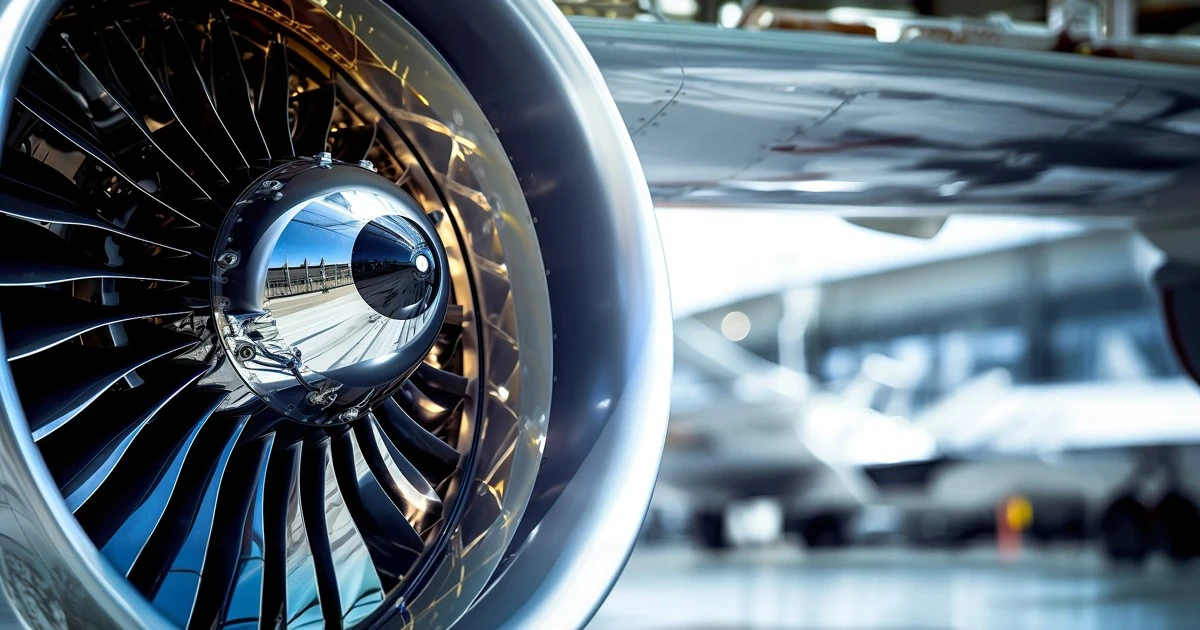
Coatings technology is the future
Invisible Armour: How Surface Coatings Forge the Future of Technology
Protective layers, often unseen, wield an extraordinary influence, turning ambitious engineering concepts into tangible realities. These sophisticated films and facings are fundamental to the operation and longevity of countless technologies, from the immense power of jet propulsion systems to the delicate intricacies of space exploration hardware. Their continuous development promises to unlock even greater efficiencies and capabilities across a spectrum of industries, pushing the boundaries of what materials can achieve. This ongoing revolution in materials science is quietly reshaping our world.
Defying the Impossible in Jet Propulsion
Jet propulsion systems stand as a pinnacle of human engineering prowess. Yet, their operational parameters present a formidable challenge. Ben Beake, who spearheads materials investigation for Micro Materials, a Welsh enterprise focused on equipment evaluation, highlights a critical paradox. The air entering these engines, he explains, reaches temperatures far exceeding 1,000 degrees Celsius. This temperature is much higher than the liquefaction threshold for the metallic alloys constituting the engine's core components, a situation that would intuitively seem catastrophic.
Ceramic Shields Against Extreme Heat
Aircraft engine designers have ingeniously navigated this thermal predicament. Their solution involves applying highly resilient ceramic surface treatments onto the engine's turbine fins. These specialised layers act as thermal barriers, insulating the underlying metal from the searing influx of superheated air. Researchers are now intensely focused on formulating even more robust coatings. The goal is to enable engines to operate at still higher temperatures, unlocking further performance gains. Cranfield University has made significant strides in developing advanced thermal barrier coatings, reducing thermal conductivity and allowing for greater temperature drops across the coating.
Hotter Engines, Enhanced Efficiency, Greener Skies
The drive to operate jet engines at increased temperatures is not merely an engineering exercise; it carries substantial environmental and economic benefits. Dr Beake elaborates that pushing the thermal operational limits leads to considerable savings in fuel consumption and a corresponding reduction in carbon dioxide emissions. He estimates that even a modest temperature increase of around 30 degrees Celsius, facilitated by improved coatings, could translate into an impressive fuel saving of approximately eight per cent. This pursuit aligns with global efforts towards more sustainable aviation.
The Unsung Significance of Surface Treatments
This capacity for radical transformation underscores the power inherent in coating technologies. These frequently disregarded protective films and facings essentially modify the operational characteristics and broaden the potential of the base materials they protect. While few people outside specialist fields may appreciate their critical role, these surface treatments are indispensable. They supercharge high-performance machinery and ensure that high-value equipment can withstand and perform optimally in the most punishing operational environments imaginable.
Micro Materials: Testing the Limits of Endurance
At Micro Materials, Dr Beake alongside his associates takes on the critical job of stressing these advanced surface layers to their absolute limits. This rigorous testing is essential to determine the true robustness and effectiveness of new formulations. The results, however, do not always align with the expectations of their clients. Dr Beake recounted an occasion previously when he had to inform a missile systems manufacturer that their proprietary coating had failed under testing. This news, he noted, prompted an abrupt and displeased departure from the clients.
Simulating a Lifetime of Wear: The "Woodpecker" Device
Beyond subjecting surface treatments to intense thermal conditions, the Micro Materials team utilizes diverse sophisticated testing protocols. One such apparatus is a device colloquially termed the "woodpecker." This instrument utilises a minuscule diamond stylus. This stylus repeatedly taps the coating at numerous random locations. The purpose of this action is to simulate accumulated stress and wear, thereby providing a reliable measure of the coating's long-term durability and resistance to mechanical fatigue under operational conditions.
Teer Coatings: Equipping Satellites for the Rigours of Space
Recently, the Welsh firm has engaged in collaborative testing with Teer Coatings, a company based in the United Kingdom. This partnership focuses on a new product intended for application on critical satellite components. These components include vital cogs and load-supports fundamental to the diverse mobile mechanisms inside a satellite's complex systems. Such protective layers are vital for mission success, demanding exceptional performance characteristics to ensure longevity and reliability in the harsh vacuum of space. Airbus Defence and Space, for instance, has developed plasma-deposited ceramic nanocomposite coatings to protect satellite parts from micrometeoroid impacts.
The Dual Challenge: Earth's Atmosphere and Orbit's Void
Xiaoling Zhang, representing Teer Coatings, described the task as particularly tricky. This surface layer is required to provide robust safeguarding to these sensitive components across two vastly different environments. Initially, it must shield them during the pre-launch phase, where they face atmospheric moisture near the earth's surface. Subsequently, and crucially, the same coating must maintain its integrity and protective qualities in orbit. There, it faces bombardment from dust particles, atomic oxygen, and pervasive space radiation. Despite these challenges, Zhang confirmed the business had successfully met the targeted protection goals.
Coatings in Orbit: Aiding Astronaut Well-being
Beyond the crucial role of protecting spacecraft hardware, advanced coatings also offer significant potential for safeguarding astronaut health during extended missions. The unique environment of space presents biological challenges that surface treatments can help mitigate. One such challenge is the accelerated growth of biofilms – dense microbial colonies – that flourish in low-gravity conditions. These can pose a serious threat within the confined habitats of space stations or future long-duration spacecraft.
The Biofilm Menace in Microgravity
Biofilms developing inside pipes and fluid systems represent a substantial issue for H2O systems or apparatus moving fluids aboard orbital habitats or prospective interstellar craft. Kripa Varanasi, a researcher from MIT, mentioned that such microbial layers have a reputation for instigating operational malfunctions. He emphasised that this is a highly undesirable scenario, particularly in the context of space missions where repair options are limited and system reliability is paramount for crew safety and mission success.
MIT's Slick Solution to Microbial Growth
Professor Varanasi and his investigation group created diverse innovative surface applications designed to render exteriors exceptionally slick. This quality makes them very capable of impeding the development of troublesome bacterial colonies. A particular application of this kind experienced thorough evaluation during a trial executed upon the ISS. The results of this orbital trial confirmed that the coating performed as intended, effectively preventing microbial adhesion and biofilm development in a microgravity environment. This success opens doors for broader applications in space and on Earth.
The Science of Slippery: Combining Solids and Lubricants
The innovative principle underpinning this anti-biofilm coating involves the careful combination of a firm substance alongside a specialised friction-reducer. This composite mixture subsequently undergoes application, often via spraying, to the internal faces of conduits or passages. The outcome of this application is an internal surface that becomes extraordinarily slick. This slipperiness drastically reduces the ability of bacteria to adhere and proliferate, thereby preventing the initial stages of biofilm formation and maintaining the cleanliness and operational integrity of the fluid systems.
LiquiGlide: From Consumer Goods to Industrial Might
Professor Varanasi earlier gained attention for developing analogous slippery coatings with more terrestrial applications. Notably, his work led to surface layers for the internal portions of dentifrice containers. This advance allows consumers to retrieve all the contents, minimising waste. Professor Varanasi alongside his associates successfully brought this adaptable coating innovation to market. They accomplished this via their affiliated enterprise, LiquiGlide, which now explores diverse industrial and consumer applications for their friction-reducing solutions.
The Underestimated Virtue of Slipperiness in Industry
The quality of being slick possesses, maybe unexpectedly, profound value in many industrial contexts, though its importance is often underappreciated. Nuria Espallargas, from the Norwegian University of Science and Technology, with her investigation associates, created an innovative surface treatment founded upon silicon carbide. This specific preparation is intended for application on equipment utilised in the demanding processes of aluminium manufacturing and repair. The aim is to reduce downtime and improve the longevity of crucial machinery.
A Non-Stick Solution for Aluminium Processing
The surface treatment using silicon carbide essentially functions as a high-performance non-stick layer, akin to those found on advanced frying pans. This characteristic signifies that stratum of liquefied aluminum, famously sticky at high temperatures, do not adhere to the expensive equipment treated with this coating. Preventing such build-up is crucial for maintaining operational efficiency and product quality. However, this specific surface layer's notable efficacy currently presents somewhat of an enigma to its creators.
Seram Coatings: Commercialising an Enigmatic Success
Professor Espallargas candidly admitted that, to be frank, they do not fully understand how it functions; the exact mechanism remains unknown at this moment. Despite this scientific enigma, the practical benefits are undeniable. Therefore, the surface treatment can be acquired for commercial use through Seram Coatings, a spin-out company established by Professor Espallargas. Atlas Machine and Supply, a US corporation involved in creating and restoring factory apparatus, put this new surface layer to the test with favorable outcomes.
Extending Tool Life, Enhancing Product Quality
Jeremy Rydberg, the head of innovation for Atlas Machine and Supply, remarked on the clear advantages seen. He mentioned the primary benefit is found in prolonging the working duration of the implements. Additionally, it helps enhance the standard of items manufactured with this treated equipment. Such enhancements directly impact operational efficiency and profitability. These improvements demonstrate the significant value that advanced coatings can bring to heavy industry.
Slashing Rebuild Costs: A Tangible Impact
Rydberg elaborated on the specific economic advantages for Atlas. Without the protective coating, the enterprise finds it necessary to reconstruct the revolving implements they utilize for processing aluminum at two-day intervals due to wear and material adhesion. This frequent maintenance and replacement activity incurs substantial annual costs, amounting to approximately 4.5 million US dollars. However, the application of the new Seram Coatings product extends the lifespan of these critical tools to an entire week, a significant improvement over the previous two-day cycle. This longevity drastically slashes the related reconstruction expenditures to approximately 1.3 million US dollars annually.
When Coatings Falter: The Reality of Imperfection
While advanced coatings can achieve remarkable feats, they do not always perform flawlessly as intended. Andy Hopkinson, the head of Safinah Group, which is a consulting business often called upon to examine coating malfunctions, observed this fact. His firm encounters numerous situations where protective layers have underperformed or failed prematurely, leading to significant problems and costs for asset owners across various sectors. Understanding these failures is crucial for improving future coating design and application.
Peeling Protections: A Car Park Conundrum
Hopkinson highlighted a recurring problem currently observed with multi-storey car parks. He mentioned that they are observing numerous difficulties where the inert flame safeguarding measure is detaching from the construction. This alludes to particular blaze-retardant colorings occasionally put onto cement components inside structures. The detachment of such coatings compromises the structure's fire safety integrity, necessitating costly remediation work and potentially posing safety risks. Proper surface preparation and material selection are critical to avoid such failures.
The Persistent Challenge of Marine Biofouling
Safinah Group has also discovered that surface layers put onto mercantile vessels fail to invariably stop crustaceans and additional aquatic organisms from adhering to the ship's underside. Such a widespread difficulty, identified by experts as biological accumulation, elevates resistance of the vessel through the water. Consequently, the vessel's propulsion unit needs to exert greater effort to keep its velocity, leading to increased fuel consumption and higher operational costs. This problem persists despite decades of research into anti-fouling technologies.
Selecting the Right Shield: A Complex Choice for Ship Owners
Despite the wide availability of sophisticated maritime surface treatments offering to fight biological accumulation, vessel proprietors fail to consistently pick the most suitable preparation for their specific vessel and operational profile. Dr Hopkinson explained that the best selection for a surface layer ought to hinge upon several critical factors. These include the maritime regions the boat usually navigates, the projected time the craft will remain stationary instead of actively moving, and the particular kinds of aquatic creatures prevalent in its operational waters. Incorrect choices can lead to suboptimal performance and increased costs.
The Exponential Cost of Coating Failures
The financial implications of rectifying such coating-related problems can be substantial, often frequently amounting to substantial sums, potentially reaching millions of pounds sterling. Mr Hopkinson observed that, typically, the initial cost of paint and its application accounts for a mere one to two per cent of a total project's budget. The significant issue, he elaborated, arises when these coatings fail. At that point, the associated rectification costs can escalate exponentially, far outweighing the initial investment in the coating system.
Nanotechnology: Revolutionising Coatings at the Atomic Scale
The advent of nanotechnology is ushering in a new era for coating development, allowing for manipulation of materials at the atomic and molecular level. Nanocoatings, which incorporate nanoparticles or are structured as nanoscale films, offer exceptional properties. These can include enhanced scratch resistance, superior corrosion protection, improved UV stability, and even self-cleaning or self-healing capabilities. Sectors like aerospace, automotive, and electronics are keenly exploring these nanocomposite coatings for their revolutionary potential.
Smart Coatings: Responding to Environmental Stimuli
A particularly exciting frontier is the development of "smart" coatings. These advanced materials are designed to respond to specific environmental stimuli, such as changes in temperature, light, pressure, or pH. For instance, self-healing coatings contain microcapsules that rupture upon damage, releasing agents to repair the compromised area autonomously. Other smart coatings can change colour to indicate temperature thresholds or material stress, providing visual warnings of potential issues. The market for these responsive materials is projected for significant growth.
Sustainable Solutions: The Drive for Greener Coatings
Growing environmental awareness and stricter regulations are powerfully steering the coatings industry towards more sustainable solutions. There is a significant push to reduce volatile organic compounds in paint formulations, leading to the wider adoption of water-based coatings and powder coatings. Furthermore, research into bio-based coatings, derived from renewable resources like plant oils, lignin, and polysaccharides, is gaining considerable momentum. These eco-friendly alternatives aim to lessen reliance on fossil fuels and minimise environmental impact.
Coatings for Renewable Energy: Protecting Green Tech
The rapidly expanding renewable energy sector presents unique challenges and opportunities for specialised coatings. Wind turbines, for example, require robust protection against erosion, corrosion, and UV degradation, particularly in harsh offshore environments. Solar panels benefit from anti-reflective coatings to maximise light absorption and self-cleaning coatings to maintain efficiency. SunDensity, an emerging firm, has developed a nano-optical coating for solar panels claimed to increase energy generation by absorbing more blue light. These protective layers are crucial for ensuring the longevity and optimal performance of green energy infrastructure.
UK Initiatives: Fostering Advanced Materials Innovation
The United Kingdom government actively supports innovation in advanced materials, including coatings, through various initiatives. Organisations like the Henry Royce Institute and the High Value Manufacturing Catapult play pivotal roles in bridging the gap between academic research and industrial application. Funding programmes, such as those managed by Innovate UK, encourage collaborative research and development projects, aiming to accelerate the adoption of new technologies and maintain the UK's position as a leader in materials science. The Centre of Expertise in Advanced Materials and Sustainability specifically fosters sustainable materials innovation.
The Economic Engine: Coatings' Industrial Impact
The paints and coatings industry represents a significant economic contributor globally. In the US alone, the industry is valued at tens of billions of dollars, providing substantial employment and driving exports. Similarly, in Canada, the sector supports a large number of jobs and is integral to numerous end-use markets, including construction, automotive, and aerospace. While facing challenges such as fluctuating raw material costs and environmental regulations, the industry's commitment to innovation, including advancements in nano-coatings and eco-friendly formulations, continues to fuel its growth and economic importance.
Overcoming Hurdles: Application and Durability Challenges
Despite remarkable progress, the practical application of industrial coatings is not without its difficulties. Ensuring proper surface preparation is paramount; failures in this initial step are a common cause of premature coating breakdown. Applying coatings uniformly on large or complex structures, such as warehouses or intricate machinery, requires specialised techniques and equipment. Environmental conditions during application, like temperature and humidity, can significantly affect curing and final performance. Addressing these challenges is crucial for realising the full potential of advanced coating technologies.
Future Horizons: The Evolving Landscape of Surface Protection
Researchers and industry experts remain optimistic about the future of coatings. They assert that numerous opportunities persist for enhancing existing surface treatments and for pioneering entirely new formulations. The ongoing development of self-healing, smart, and sustainable coatings promises to further revolutionise material performance. These advancements might significantly elevate the working effectiveness and durability of machinery, infrastructure, and consumer products in the years to come. The field continues to evolve, driven by demands for greater durability, enhanced functionality, and improved environmental compatibility, ensuring that coatings remain a critical enabling technology across countless applications.
Recently Added
Categories
- Arts And Humanities
- Blog
- Business And Management
- Criminology
- Education
- Environment And Conservation
- Farming And Animal Care
- Geopolitics
- Lifestyle And Beauty
- Medicine And Science
- Mental Health
- Nutrition And Diet
- Religion And Spirituality
- Social Care And Health
- Sport And Fitness
- Technology
- Uncategorized
- Videos