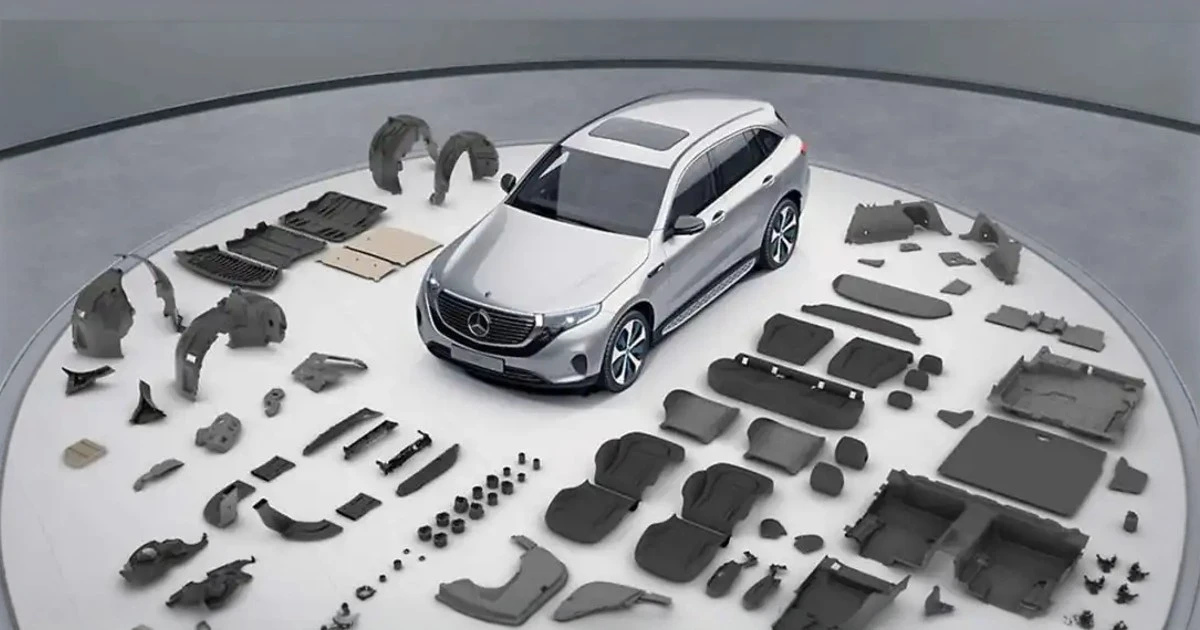
Lightweighting: The Evolution of Automotive Materials
Revolutionizing Automotive Materials: A Quest for Lighter, Safer Vehicles
Modern automotive engineering prioritizes lightweighting to enhance fuel efficiency and extend the range of electric vehicles. A crucial component of this is the development of superior steel alloys. Consequently, manufacturers relentlessly pursue stronger, lighter materials to achieve both safety and efficiency goals.
Ancient Inspirations, Modern Innovations
The pursuit of exceptional steel dates back millennia. Ancient Indian metallurgists, through a combination of adept craftsmanship and fortunate circumstances, discovered wootz steel. This remarkable material, produced by heating iron in charcoal-filled clay containers, rapidly became a highly valued commodity. Centuries later, modern automakers employ advanced techniques like electric arc furnaces and sophisticated stamping processes. These cutting-edge methods enable precise tailoring of steel properties, thereby enhancing vehicle safety and minimizing weight.
Economic and Environmental Imperatives
Reducing a vehicle's weight by even a single pound yields significant fuel cost savings over its operational life. The lighter the vehicle, the lower the fuel consumption, leading to substantial cost savings for the owner. Consequently, the economics of lightweighting are compelling. Furthermore, this reduction in mass benefits the environment by decreasing the vehicle's overall carbon footprint. This dual emphasis on cost-effectiveness and environmental responsibility is crucial.
The Electric Vehicle Conundrum
The shift toward electric vehicles (EVs) underscores the importance of lightweight materials. While EVs boast zero tailpipe emissions, they often weigh more than their gasoline counterparts. This increased mass compromises range and, potentially, safety. Therefore, the development of lighter materials is paramount to enhancing EV performance and range, ensuring both safety and sustainability.
The Evolution of Automotive Steel
Prior to the mid-20th century, auto bodies predominantly used relatively heavy soft steel. The 1970s oil crises and Ralph Nader's seminal work on automotive safety significantly influenced the industry. These factors emphasized the need for both stronger and lighter steel to enhance fuel efficiency and passenger safety. Subsequently, over the past few decades, significant progress has been made in developing advanced high-strength steels, tailored for diverse applications within the vehicle's structure.
Crafting Superior Steel: A Microstructural Perspective
The key to superior steel lies in understanding its microstructure. The arrangement of different steel phases directly impacts its properties. Some phases contribute hardness, while others enhance ductility, enabling the material to withstand bending and deformation without fracturing. Consequently, manipulating heating and cooling processes allows steel manufacturers to precisely control the microstructure of steel, leading to various grades tailored for specific automotive needs.
Advanced High-Strength Steel: Generations of Progress
The quest for superior steel has yielded three generations of advanced high-strength steel. The first generation, dominant in the 1990s, offered a balanced combination of strength and ductility. However, the subsequent second generation, utilizing more intricate alloys, presented manufacturing challenges and higher production costs. The current third generation, now gaining widespread application, leverages refined heating and cooling techniques. This approach results in stronger and more malleable steels compared to previous iterations, often surpassing the strength of earlier generations by a considerable margin, while potentially improving the affordability.
Cooling Time: A Critical Determinant
Cooling time emerges as a critical factor in steel production. Quenching, the rapid cooling process, arrests internal structural transformations. This rapid cooling method fixes the internal structure of the steel before further changes occur, leading to enhanced strength and stability. The precise control of cooling rates is essential for attaining desired atomic arrangements, thereby achieving optimal material properties. The carefully controlled cooling rate directly impacts the resulting microstructure and the subsequent performance of the steel.
Superheating and Rapid Cooling: The Modern Approach
For critical structural components like side panels and pillars, superheating is employed, often involving boron and manganese. This process heats the metal above 850 degrees Celsius, making it malleable. Subsequently, the superheated steel is rapidly transferred to a mold or die for shaping and then rapidly cooled, locking in the desired shape and properties. The combination of high temperatures, precise shaping, and controlled cooling ensures the resultant steel component has the required strength, durability, and resilience to withstand various operating conditions.
Transformation-Induced Plasticity: Tailoring Material Properties
Transformation-induced plasticity represents a sophisticated approach to steel refinement. This process involves heating the steel, cooling it to a specific intermediate temperature, holding it there for a controlled duration, and then quickly quenching it. The outcome is a unique microstructure characterized by clusters of austenite, a softer ferrite matrix, with regions of harder bainite and martensite. This diverse microstructure bestows exceptional energy absorption capacity, rendering the steel exceptionally suitable for components like bumpers and structural pillars.
Alloying for Enhanced Performance
Alloying, the addition of other elements to steel, significantly enhances its properties. Pioneering figures like Henry Ford recognized the benefits of alloying steel with vanadium to improve performance, particularly in the Model T. Modern practices continue refining steel alloys to achieve enhanced strength, improved lightness, and increased corrosion resistance. The deliberate incorporation of specific alloying elements allows for the precise tailoring of various material properties, significantly enhancing the functionality of the steel.
Shaping Metal: Tube Hydroforming
Tube hydroforming stands as a revolutionary method for creating complex metal shapes. This process involves precisely bending metal into desired shapes through high-pressure injection of fluids into a tube. The fluid pressure expands the tube into the shape of a surrounding mold, thereby creating intricate components without the need for welding two halves together. This approach boosts efficiency and reduces costs compared to traditional fabrication techniques.
Modern Alloys and Materials
Beyond steel, the pursuit of lighter and stronger materials has led to the exploration of titanium and niobium alloys, which increase strength by stabilizing metal microstructure. Consequently, the introduction of niobium alloys represents a significant advance in physical metallurgy. This highlights the ongoing development and utilization of advanced materials and alloys to achieve optimal vehicle performance.
Computational Power: Revolutionizing Material Development
The advent of powerful computing capabilities has dramatically altered the landscape of material development. Now, engineers can use sophisticated simulations to explore and evaluate various materials and processes at the atomic level, drastically accelerating the development cycle. This approach bypasses the time-consuming and costly trial-and-error methods of the past. Consequently, computer modeling allows engineers to test various scenarios and materials virtually, without the need for extensive physical experimentation, significantly reducing development time and costs.
The Institute for Advanced Composites Manufacturing Innovation: A Hub for Innovation
The Institute for Advanced Composites Manufacturing Innovation (IACMI) exemplifies the collaborative approach to innovation. Founded in 2015 with a substantial grant, IACMI serves as a critical nexus for the automotive industry. This institute fosters the development, testing, and scaling up of innovative processes and products, aiming to propel the industry forward. IACMI is specifically dedicated to addressing the complex challenges in advanced composites manufacturing and to fostering collaborative solutions between industry partners, research institutions, and government agencies.
Sustainable Alternatives: Beyond Lightweighting
The pursuit of lightweight materials is essential, but sustainability extends beyond reducing weight. A complete life cycle assessment (LCA) is imperative, encompassing the environmental impact of material sourcing, manufacturing processes, and end-of-life disposal. This holistic approach demands the consideration of the entire lifecycle of a vehicle, from the extraction of raw materials to the recycling and disposal of components. Consequently, the industry must prioritize closed-loop systems that minimize environmental impact at each stage of a vehicle's journey.
Addressing Plastic's Environmental Impact
Plastics, while offering cost-effectiveness and a high strength-to-weight ratio, present significant environmental concerns. The increasing incorporation of plastics in vehicles, rising from less than 100 pounds per vehicle in the 1960s to nearly 350 pounds in 2017, highlights the need for more sustainable alternatives. Consequently, the growing reliance on plastics necessitates solutions to manage the environmental impact of end-of-life components.
Developing Sustainable Materials and Processes
Researchers are actively seeking stronger, lighter, and more environmentally friendly plastics. Concurrent efforts are focused on developing processes that promote the efficient recycling of plastic and other complex materials. This necessitates the development of innovative solutions for the handling and processing of post-consumer vehicle components, including automotive shredder residue. These efforts aim to mitigate the environmental footprint of plastics in automotive manufacturing and promote the circular economy concept.
Leveraging Carbon Fiber for Structural Integrity
Carbon fiber composites provide a promising path toward lightweighting while preserving structural integrity. Their application extends beyond decorative elements, increasingly finding use in load-bearing components, such as structural underbody parts. Consequently, this strategic integration of carbon fiber reduces the reliance on heavier metals, contributing to significant reductions in vehicle weight.
The Significance of Government Policies and Consumer Demand
Government policies and consumer choices play a vital role in driving this transformation. Incentivizing the use of sustainable materials, promoting research in sustainable manufacturing, and implementing strict regulations on emissions and waste management will accelerate the shift towards greener practices. Consumers can influence the market by prioritizing eco-conscious vehicle options. This dual approach of proactive policy and informed consumer demand is crucial for advancing the industry towards a truly sustainable future.
Looking Ahead: Future Research Directions
Future research must focus on developing innovative materials, refining manufacturing processes, and enhancing recycling technologies. This research will be crucial in achieving a fully circular economy for automotive components. Furthermore, research into developing sustainable alternatives to common plastics and developing processes for efficient and cost-effective recycling are vital for achieving a truly circular economy and sustainable practices in the automotive industry.
The Interplay of Design and Materials: A Synergistic Approach
The pursuit of lightweight, strong, and sustainable vehicles demands a synergistic approach, seamlessly integrating material science advancements with innovative design strategies. Simply substituting materials without considering the overall vehicle architecture is insufficient. A profound understanding of material interactions within the vehicle's structure is crucial. Consequently, engineers must meticulously select materials for specific components, considering factors like stress distribution, impact absorption, and aesthetic considerations. This integrated approach optimizes design, maximizing the benefits of new materials and manufacturing processes.
The Entire Lifecycle: From Cradle to Grave
A holistic perspective extends beyond individual component optimization. The entire lifecycle of a vehicle, from material extraction to end-of-life disposal, must be meticulously assessed to minimize environmental impact. This means evaluating each stage for potential environmental repercussions, from the extraction of raw materials to the eventual recycling or disposal of components. Ultimately, the goal is to establish a closed-loop system, minimizing waste throughout the vehicle's lifespan.
Government Policies and Incentives: Driving Sustainability
Governments hold significant sway in shaping the industry's trajectory toward sustainability. Incentivizing the use of recycled materials, promoting research and development in sustainable manufacturing, and enacting stringent regulations on emissions and waste disposal are critical steps. Furthermore, proactive government policies should foster collaboration between industry players, academic institutions, and regulatory bodies, accelerating the development of comprehensive solutions to reduce the environmental footprint of vehicles.
Consumer Awareness and Demand: Driving Change
Consumer awareness and demand play a pivotal role in driving the adoption of sustainable practices. Educating the public about the environmental benefits of lightweight vehicles, emphasizing the importance of material selection, and showcasing the impacts of end-of-life vehicle management are crucial steps. Transparency in material sourcing, manufacturing, and recycling processes fosters consumer trust, encouraging the adoption of environmentally conscious vehicle choices. Ultimately, consumer demand, coupled with effective policies, shapes the market toward more sustainable options.
Research and Development: The Foundation for Progress
Ongoing research and development are essential for a sustainable automotive future. This includes exploring innovative materials with unparalleled strength-to-weight ratios, minimizing environmental impact, and refining manufacturing processes to maximize efficiency. Furthermore, developing cost-effective and efficient recycling technologies for end-of-life vehicles will create a closed-loop system crucial for long-term sustainability. Consequently, this continuous cycle of research and development drives progress toward environmentally friendly solutions.
Human Factors and Ergonomics: Prioritizing Safety
Safety must remain paramount throughout the design process. Enhanced performance and fuel efficiency must not come at the expense of safety. Incorporating human factors, encompassing ergonomics and intuitive interfaces, is essential. The design must prioritize passenger comfort and ease of operation. Consequently, understanding and addressing user needs is integral to ensuring safe and enjoyable vehicle use.
Global Collaboration: Fostering Innovation and Knowledge Sharing
The complexities of sustainable vehicle production necessitate global collaboration and knowledge sharing. International cooperation between research institutions, manufacturers, and policymakers is essential to accelerate innovation and standardization. Sharing best practices and fostering collaborations across borders will accelerate the adoption of sustainable materials and practices, accelerating the transition toward a more sustainable automotive future.
Beyond the Vehicle: The Wider Picture
Sustainability encompasses more than just the vehicle itself. Examining the entire supply chain, from material sourcing to manufacturing and disposal, provides a holistic perspective. Furthermore, integrating sustainability into the broader infrastructure, encompassing charging networks and vehicle maintenance protocols, will be crucial to a fully sustainable transportation system. This wider perspective recognizes the interconnectedness of individual actions and systemic changes required for a more sustainable future.
The Sustainable Automotive Future: A Path Towards a Greener Tomorrow
The automotive industry stands at a critical juncture, poised to transition from an era of dependence on fossil fuels to one of sustainable mobility. This transformation demands a multifaceted approach, seamlessly integrating material science advancements, innovative design strategies, proactive government policies, and informed consumer choices. This transition is not merely a trend; it's a fundamental shift towards a more environmentally conscious future.
The Convergence of Science, Technology, and Policy
The convergence of scientific progress in materials science and technological breakthroughs in manufacturing offers the potential for groundbreaking vehicles. However, these innovations must be underpinned by proactive government policies. Incentivizing the use of sustainable materials, promoting research in sustainable manufacturing, and implementing stringent regulations on emissions and waste management are crucial. Consequently, a supportive policy framework is essential for encouraging sustainable practices and driving the industry towards a more eco-friendly future.
Consumer Responsibility and Market Shaping
Consumer awareness and demand are potent forces shaping the automotive market. Educating consumers about the environmental impact of their choices and highlighting the benefits of sustainable vehicles is critical. Transparency in material sourcing, manufacturing, and recycling processes will foster consumer confidence and encourage the adoption of eco-friendly options. Therefore, a strong synergy between consumer awareness and government policies will accelerate the adoption of sustainable practices.
The Holistic Approach: Embracing a Circular Economy
A truly sustainable future requires a holistic approach, considering the entire lifecycle of a vehicle, from material sourcing and manufacturing to end-of-life disposal and recycling. This holistic perspective envisions a circular economy where materials are reused and recycled, minimizing waste and maximizing resource utilization. Consequently, this shift emphasizes reducing waste generation and optimizing resource management.
Collaboration and Knowledge Sharing: A Global Imperative
The complexity of creating sustainable vehicles necessitates global collaboration. International partnerships between research institutions, manufacturers, and policymakers are essential to accelerate innovation and promote standardization. Sharing best practices and fostering international cooperation will significantly accelerate the adoption of sustainable materials and practices across the globe. This collaboration is crucial for overcoming the challenges and sharing knowledge essential for rapid progress.
Driving Innovation and Technological Advancement
Continuous research and development are paramount for achieving breakthroughs in sustainable materials, manufacturing processes, and recycling technologies. Innovation must encompass exploring novel composites, refining existing alloys, and developing more efficient recycling methods. Consequently, a commitment to ongoing research will be crucial for achieving significant advancements in the field.
Beyond the Vehicle: A Broader Perspective
A sustainable automotive future extends beyond the vehicle itself. A comprehensive approach also encompasses the entire supply chain, from material sourcing and manufacturing to end-of-life disposal. Furthermore, integrating sustainability into the wider infrastructure, including charging networks and vehicle maintenance protocols, is critical for realizing a truly sustainable transportation system. This expanded perspective underscores the interconnectedness of individual actions and systemic changes for environmental sustainability.
The Legacy We Leave Behind: Building a Better Tomorrow
The automotive industry holds a responsibility to shape a better tomorrow for future generations. This commitment extends to designing vehicles not only as efficient and safe but also as environmentally responsible. This transition toward sustainable mobility is not merely a trend but a fundamental shift toward a more sustainable transportation future. Consequently, this imperative to preserve the environment for generations to come is critical. This transition from fossil fuels to sustainable mobility is a defining moment for the automotive industry.
Conclusion
The automotive industry's journey, from its humble beginnings to the present, has been remarkable. The evolving landscape highlights the necessity of adopting sustainable mobility, necessitating a continuous commitment to innovation, collaboration, and a holistic approach. This critical shift necessitates a harmonious blend of technological advancements, policy support, consumer awareness, and a global vision for a sustainable future. Only by embracing this multifaceted approach can we truly shape a greener tomorrow for generations to come.
Recently Added
Categories
- Arts And Humanities
- Blog
- Business And Management
- Criminology
- Education
- Environment And Conservation
- Farming And Animal Care
- Geopolitics
- Lifestyle And Beauty
- Medicine And Science
- Mental Health
- Nutrition And Diet
- Religion And Spirituality
- Social Care And Health
- Sport And Fitness
- Technology
- Uncategorized
- Videos