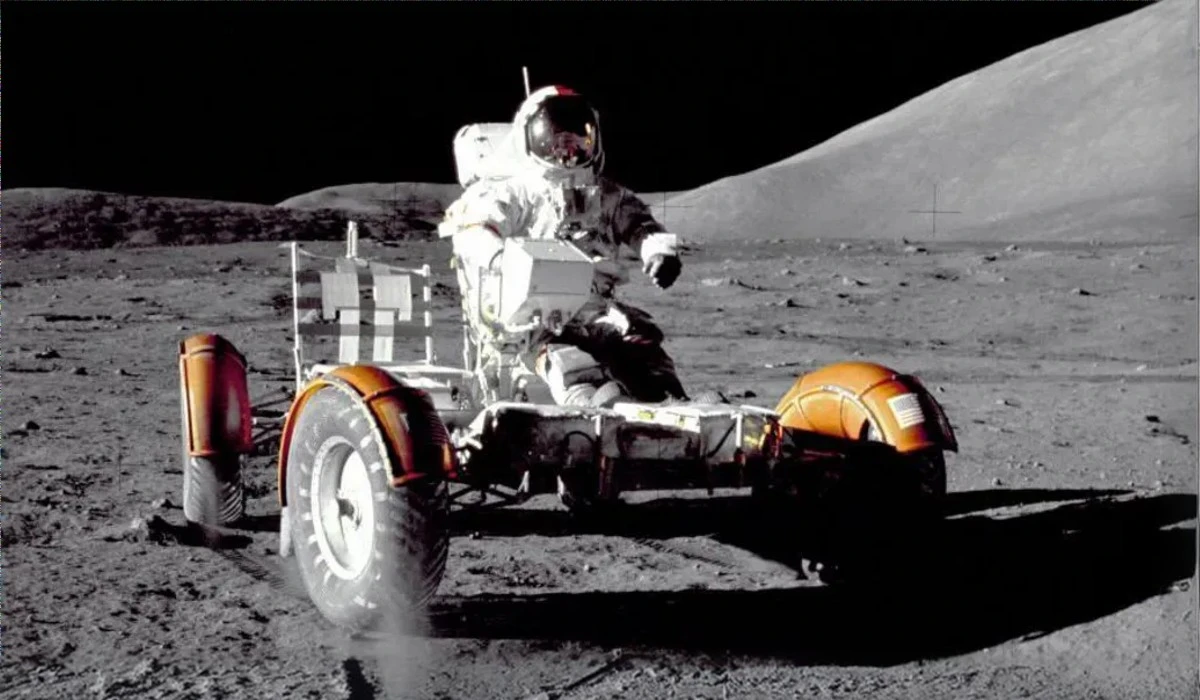
Tyres Forging New Paths For Lunar Rovers
Forging New Paths: Designing Tyres for Lunar and Martian Terrains
Humanity embarks upon a renewed chapter of cosmic journeys. Ventures return to the lunar environment, after a hiatus exceeding fifty years, and subsequent missions towards Mars, demand a complete overhaul of established technologies, including the essential wheel. The notion of a tyre failing millions of kilometres from Earth is entirely unacceptable. This stark reality compels engineers and scientists to pioneer groundbreaking tyre systems capable of enduring the harsh conditions awaiting on other worlds.
The Unyielding Threat of Tyre Failure in Space
Florent Menegaux, who leads the French tyre-producing firm Michelin, clearly articulates the absolute necessity for dependability. He asserts that a tyre rupture represents an intolerable setback during missions beyond Earth. The operational history of previous uncrewed explorations highlights this critical point. Mars, specifically, offers a formidable trial for any equipment. Its surface is punishing, a vista of jagged stones and fine, abrasive particles. This reality was demonstrated by Nasa's exploratory vehicle, Curiosity.
A single Earth year following its 2012 arrival on the Red Planet, Curiosity's six inflexible, metallic wheel assemblies showed clear signs of degradation. Perforations and fissures compromised the metal structures, a direct consequence of the severe Martian landscape. These particular wheels, not engineered for the exact type of ground encountered, brought into sharp focus the pressing requirement for more robust and versatile tyre concepts. Upcoming expeditions, particularly those transporting human teams, cannot risk such weaknesses. The return trip from Mars, should a vital part like a tyre malfunction, becomes an impossible undertaking.
Artemis: Charting a New Course for Moon Exploration
The Artemis initiative, from the United States, is at the vanguard of returning human explorers to Earth's natural satellite. Current timetables project a crewed touchdown, feasibly around 2027, with later expeditions broadening capabilities for investigating the Moon. Artemis V, anticipated for March 2030, will distinctively feature the deployment of a new Lunar Terrain Vehicle (LTV) for investigating the southern polar area of the Moon. This undertaking represents a substantial advancement in lunar surface activities.
Astronauts on Artemis missions will travel considerably greater distances than their Apollo mission counterparts. Throughout the six Apollo touchdowns occurring from 1969 to 1972, lunar vehicles never journeyed more than 40 kilometres (roughly 25 miles) from their touchdown locations. The LTV, in contrast, must traverse immensely larger areas, facilitating more prolonged and intricate scientific journeys. This expanded operational scope calls for exceptional resilience and capability from its wheel systems.
Michelin's Bold Aspirations for Lunar Mobility
Michelin, an enterprise with an extensive legacy in tyre development, readily accepts this significant undertaking. Sylvain Barthet directs Michelin's initiative for air-free lunar wheels in Clermont Ferrand, a city in central France. He shares their ambitious aim: to achieve 10,000 kilometres of travel within a decade. This number starkly conveys the substantial increase in performance expected for lunar transport. The tyres must endure continuous operation over ten years, greatly surpassing the brief excursions of the Apollo period.
This forward-looking objective demands a complete change in tyre engineering philosophy. Michelin applies its deep knowledge of composite substances and novel production methods, such as 3D printing, to create solutions without air. The organization evaluates prototypes on volcanic landscapes near Clermont, since the fine-grained ground there closely simulates lunar regolith. Power conservation also remains a key factor, particularly for activities in shadowed zones where sunlight for energy is scarce.
Image Credit - BBC
Nasa's Blueprint for a Lasting Lunar Foothold
Nasa's goals reach further than brief excursions. Dr Santo Padula, an engineer at Nasa's John Glenn Research Centre located in Cleveland, Ohio, possesses a doctorate in materials science. Dr Padula underscores this change in perspective, stating they are not considering brief, week-long operational windows but are instead planning for several decades of service. This concept of an enduring human settlement on the Moon, possibly via an Artemis Base Camp, calls for strong, durable systems, including dependable rovers.
The LTV, a vital element of this planned infrastructure, will assist astronauts in surveying broader regions, moving scientific apparatus, and gathering specimens. In the intervals between human-crewed expeditions, Nasa intends for the LTV to function through remote control, thereby continuing scientific inquiries. This capacity for dual operation further emphasizes the requirement for remarkably tough and adaptable tyres, able to withstand the lunar conditions for lengthy durations without needing direct human intervention.
The Severe Temperature Challenge
A primary difficulty when creating technology for use on the Moon, especially concerning tyres, involves the vast differences in temperature. Near the Moon's poles, the focus of upcoming Artemis missions due to possible water ice reservoirs, temperatures can drop below minus 230 degrees Celsius. Such intensely cold conditions are close to absolute zero, the theoretical state where atomic activity halts. This presents a major hurdle for materials engineering.
Conversely, locations under direct solar illumination can experience temperatures as high as 120 degrees Celsius. Tyres are required to preserve their structural soundness and pliability across this wide thermal variation. The absence of a significant lunar atmosphere means heat does not get retained or moderated as on Earth, causing these extreme shifts. Conventional rubber materials, for example, would turn fragile and glass-like in such intensely low temperatures.
Materials Under Extreme Cold Conditions
Profound cold dramatically alters the characteristics of materials. Dr Padula describes a fundamental problem, explaining that without atomic movement, it is very difficult for a substance in a position to distort and then recover its form. Tyres must possess the capacity to flex upon encountering objects like stones and then rapidly revert to their initial configuration for effective travel. This springiness is vital for maintaining grip and ensuring smooth passage over uneven lunar ground.
Should a tyre substance become excessively stiff due to cold, it loses the ability to absorb shocks properly. This inflexibility might lead to cracking or breaking. Additionally, if the material changes shape permanently instead of returning to its intended form, the tyre’s ability to roll well decreases substantially. Such poor performance would cause higher energy use, a major concern for rovers powered by batteries operating far from any energy supply or during extended lunar nights.
The Issue of Irreversible Deformation
An irreversible change in the shape of a lunar tyre creates significant operational difficulties. Dr Padula points out that if a tyre undergoes permanent distortion, its rolling capability is compromised, leading to problems with power depletion. Inefficient rolling necessitates that the rover's motors expend more energy, more rapidly depleting vital battery power. This could limit the scope of exploration and the length of scientific undertakings. Consequently, chosen materials must demonstrate superior shape retention and toughness.
A tyre's capacity to consistently flex over impediments and then regain its form is essential. This characteristic, termed elasticity, guarantees the vehicle stays in contact with the ground for best possible grip and also absorbs jolts, thereby safeguarding the rover and its delicate scientific tools. Scientists are investigating diverse metallic compounds and sophisticated polymers that can preserve these crucial mechanical attributes even when subjected to severe lunar environmental factors.
Increased Loads, Intensified Stress
Forthcoming lunar explorations will involve considerably more substantial and heavier items than the minimal-weight rovers Apollo missions utilised. The Apollo Lunar Roving Vehicles were engineered for brief trips and carried little equipment. The Artemis period, by contrast, anticipates "more substantial scientific platforms and mobile living quarters that progressively increase in size," as stated by Dr Padula. These advanced rovers need to convey more astronauts, a wide array of scientific gear, and possibly elements for building lunar outposts.
This growth in mass directly results in heightened pressure on the wheel assemblies and tyres. The substances employed must not only endure the temperature extremes and the scouring lunar dust but also bear these considerably heavier burdens without any reduction in performance or operational life. This stipulation further restricts the available suitable materials and stimulates innovation in structural engineering to achieve the best possible strength-to-mass ratios.
The Martian Gravity Factor
The difficulty of bearing substantial burdens becomes even more pronounced on Mars. While the Moon's gravitational pull is roughly one-sixth of Earth's, Mars has a gravitational force approximately twice that of the Moon, or about 38% of Earth's. This signifies that a rover and its contents will have a notably greater weight on Mars compared to the Moon, imposing a proportionally larger load on its tyres.
Specialists creating tyres for Martian use must consider this augmented gravitational effect. The tyre's internal framework must be sufficiently strong to manage the extra weight without failing or excessively changing shape. Insights gained from the wheel damage on Curiosity, alongside the stronger gravity, guide the engineering choices for upcoming Martian exploratory vehicles, like the Rosalind Franklin rover from the ESA.
Looking Back at Apollo's Mesh Wheel Design
The Apollo lunar exploration vehicles used a distinct wheel system for that period. These assemblies featured a woven structure of piano wire coated with zinc. Chevrons made of titanium offered grip on the Moon's dusty terrain. Though inventive, these wheels were meant for restricted operation; for instance, the Apollo 17 rover travelled a total of about 35 kilometres. The LTV for Artemis aims for operational ranges far exceeding this.
The Apollo wheel concept provided a light and reasonably effective system for the brief missions of that time. Nevertheless, the requirements of extended exploration, covering greater distances, and carrying heavier items make a move away from this older technology necessary. The Apollo experience, however, still offers useful information on how metallic components behave in the lunar environment, which aids current developmental work.
Why Conventional Rubber Is Unsuitable for Space
Standard rubber tyres, common on Earth, are not appropriate for the demanding conditions of outer space. The vast temperature changes on the Moon would cause rubber to either decompose or transform into a delicate, glass-like material, making it unusable. Moreover, powerful cosmic and solar radiation, without the protection of a significant atmosphere, would break down the polymer structures in rubber, further weakening its structural soundness and ability to flex.
Beyond temperature and radiation, the vacuum of space also introduces difficulties. Rubber tyres depend on internal air pressure to maintain their form and function. Any breach would result in immediate deflation and total failure. Consequently, designs without air, or non-pneumatic systems, are vital for trustworthy performance on the Moon and Mars. This situation has prompted scientists to investigate entirely new categories of substances.
Image Credit - BBC
The Search for Exceptionally Strong Materials
Considering how traditional substances like rubber perform poorly, the development of air-free tyres for space has turned towards metallic compounds and advanced plastics or composites. These substances present the likelyhood of superior endurance against severe temperatures, radiation, and the wearing effect of lunar dust. Pietro Baglion, who directs the team for ESA's Rosalind Franklin Mars rover undertaking, affirms that materials based on metal or carbon fibre are generally chosen for these kinds of wheels.
The criteria for selection are exacting. Substances need to be light yet robust, pliable yet resistant to permanent alteration of shape, and able to keep these characteristics across temperature shifts of hundreds of degrees. The creation process includes thorough testing in simulated lunar settings, using vacuum chambers and thermal cycling assessments, to confirm that the selected materials can endure the decade-long operational periods now being planned.
ESA's Rosalind Franklin and Substance Choices
The Rosalind Franklin rover from the ESA, an element of the ExoMars initiative, also needs dependable wheel technology for its intended 2028 journey to Mars. Although Mars has its own specific difficulties, such as a tenuous atmosphere and different soil makeup than the Moon, the basic requirement for long-lasting, air-free tyres is constant. The rover has the capability to travel several kilometres and to drill as deep as two metres beneath the Martian ground to look for evidence of previous life.
The engineering of the Rosalind Franklin rover includes six wheels; each can steer and pivot independently, facilitating a "wheel-walking" type of movement to traverse challenging ground. This sophisticated mobility emphasizes the critical nature of trustworthy wheel units. Material selections for these wheel assemblies concentrate on metals and composites that can endure the Martian conditions, encompassing temperature variations and abrasive dust, while also supporting the rover’s scientific instruments.
Nitinol: The Metal with a Memory
A particularly hopeful substance for space-bound tyres is nitinol, a compound primarily of nickel and titanium. This "shape memory alloy" displays extraordinary characteristics. Earl Patrick Cole, head of The Smart Tire Company, clarifies that when these metals combine, they form a "metal that acts like rubber, capable of bending in numerous distinct types, and it will invariably return to its initial configuration." This capacity to regain its original form after being misshapen is vital for tyre toughness.
Dr Santo Padula characterizes nitinol as a substance with "game-changing" possibilities. In addition to its remarkable elasticity, nitinol can take in and give off energy as its internal structure changes. This trait, Dr Padula proposes, could even provide answers for temperature control systems in space. The Smart Tire Company is actively creating tyres based on nitinol, advancing technology first investigated for Martian vehicles.
The Smart Tire Company's Nitinol Progress
The Smart Tire Company, led by Earl Patrick Cole, pioneers the commercial use of nitinol tyre technology, which originated from research supported by Nasa. Cole engaged in a Nasa scheme for entrepreneurs to identify earthly uses for the super-elastic tyre system created for Martian rovers. This effort has resulted in the creation of air-free bicycle tyres using nitinol, anticipated to be exceptionally resilient, though commanding a higher price than standard tyres.
The enterprise intends to apply this technology to robust tyres for motorcycles, aiming at positions with substandard road surfaces. Despite these terrestrial uses, Cole's main goal continues to be a role in humankind's voyage back to the Moon, picturing his firm's sophisticated tyres traversing the lunar landscape. The special qualities of nitinol present a strong answer to the difficulties of movement beyond Earth.
Image Credit - BBC
Michelin's Investigation into Advanced Plastics
Although nitinol demonstrates considerable potential, Michelin is concurrently examining alternative materials. Sylvain Barthet from Michelin posits that a substance more like a high-specification plastic or composite could be better suited for tyres designed for extensive travel on the Moon. Michelin’s latest lunar wheel design, revealed in 2024, employs composite substances engineered for a ten-year operational life, able to transport two astronauts and survey distant regions.
These sophisticated plastics and composites allow engineers to achieve a precise mix of pliability, robustness, and endurance against the lunar conditions. Michelin's design incorporates an intricate arrangement of curved spokes that support a broad, solid rim. The aim is to achieve low rolling resistance, thereby conserving rover battery power, and to ensure good grip on unconsolidated surfaces. The company’s considerable background with earth-based tyre materials and cutting-edge production methods, including 3D printing for these particular uses, guides this line of development.
Bridgestone's Nature-Inspired Camel Foot Design
Japanese tyre firm Bridgestone has embraced an intriguing method drawing from nature: biomimicry. Their technical teams analyzed camel foot structures to guide their lunar tyre concepts. Camels have soft, fat-rich footpads that efficiently spread their body mass across an enlarged contact patch. This biological feature stops their feet from subsiding into shifting desert sand, a concept very applicable to the fine regolith that blankets the Moon.
Bridgestone’s idea translates this natural mechanism into an engineered tyre. It incorporates a substance similar to felt for its gripping surface, intended to improve hold on the fine lunar particles. The wheel structure itself includes slender, pliable metallic spokes. This arrangement seeks to replicate the camel's capacity to manage load distribution and sustain grip on difficult, loose ground.
How Flexible Spokes Function
The essence of Bridgestone's concept is found in its pliable metallic spokes. As the lunar vehicle's mass presses onto the tyre, these spokes yield. This yielding motion assists in spreading the force over a more extensive area of contact with the lunar terrain. By enlarging this contact zone, the tyre has a reduced tendency to excavate and become immobilized in the Moon's superficial covering of broken rock and fine particles, termed regolith.
This engineering prioritizes the ability to float over and grip surfaces, which is essential for moving across the erratic and frequently soft lunar ground. This is particularly true in the permanently shadowed areas of the south pole, where ice might be intermingled with the regolith. Bridgestone, akin to Michelin, assesses its developmental models in settings that replicate lunar conditions, specifically upon the Tottori Sand Dunes located in western Japan, to simulate the Moon's ground characteristics. Toyota is also working with JAXA on a crewed lunar vehicle, the Lunar Cruiser, set to use Bridgestone’s metal tyre system.
Nasa's Pivotal Tyre System Choice
With multiple firms creating novel solutions, Nasa confronts a weighty decision. Michelin and Bridgestone are prominent entities within separate alliances that have shown their developed tyre systems to Nasa personnel at the John Glenn Research Centre. Venturi Astrolab, based in California, is another enterprise that put forward a concept for the Lunar Terrain Vehicle. Nasa anticipates announcing its choice, possibly opting for one supplier or merging features from several concepts to achieve the best LTV design.
Nasa's LTV Services initiative intends to obtain the rover as a contracted service from the private sector, encompassing its design, creation, and functioning through to 2039. The selected LTV must manage the severe environments at the Moon's southern polar region, incorporating sophisticated energy management, autonomous navigation features, and advanced communication and guidance technology. The tyres form a critical base for this high-tech vehicle.
Earth-Based Tests: Replicating Lunar Conditions
Before any tyre makes contact with lunar regolith, comprehensive assessments take place in terrestrial locations that simulate the Moon's environment. Michelin employs a volcanic site near Clermont in France, where the fine-grained volcanic material closely mirrors lunar dust, to evaluate its test rovers. In a similar vein, Bridgestone performs evaluations on the Tottori Sand Dunes in western Japan; the fine sand there offers a comparable loose base. These Earth-situated simulations are vital for judging tyre capability, endurance, and grip.
Such simulations enable engineers to witness how various designs behave on demanding terrains, pinpoint possible weaknesses, and perfect their ideas prior to undertaking the huge cost and intricacy of a space voyage. This type of testing helps in understanding how the tyres will manage dust penetration, abrasion, and the distinct mechanical nature of lunar soil.
ESA's Aspirations for Independent Rover Development
The ESA is likewise contemplating the creation of its own exploratory vehicles for upcoming missions, either separately or in partnership with other global initiatives. Sylvain Barthet from Michelin mentioned that ESA is looking into this avenue. This indicates a wider international enthusiasm for lunar discovery and the establishment of autonomous capabilities. An ESA-directed rover undertaking would further encourage innovation in fields such as tyre technology throughout Europe.
These kinds of projects add to an expanding network of space exploration technology. Should Europe move forward with its own rover, it would probably utilize the knowledge of European firms and research bodies. This could result in varied design approaches and material selections for essential parts like wheels, thereby increasing the diversity of technological methods for movement on other celestial bodies.
Lunar Dust: Abrasive Particles as a Foe
A continuous difficulty for all hardware on the lunar surface, particularly for moving components like tyres, is the presence of lunar dust, or regolith. In contrast to terrestrial dust, which is frequently smoothed by weathering, lunar dust particles are pointed, glass-like, and abrasive. This is due to ongoing micrometeoroid impacts in the vacuum. This dust adheres to all surfaces because of electrostatic attraction and can penetrate seals, wear down materials, and impair thermal protection layers.
The Apollo astronauts encountered many difficulties with lunar dust. It led to deterioration of spacesuits, problems with apparatus, and even breathing discomfort. For tyres, this abrasive particulate matter can hasten wear, diminish grip if it obstructs tread designs, and possibly harm the pliable elements of air-free wheel systems. Countering the impacts of lunar dust is a vital engineering focus for hardware intended for long use on the Moon. Current investigations examine dust-resistant coatings and materials that resist abrasion.
Energising a New Fleet of Rovers
Forthcoming lunar exploratory vehicles, the Artemis LTV included, will require strong power systems to facilitate prolonged missions, carry heavier items, and operate advanced tools. While early Apollo rovers depended on batteries that could not be recharged, future vehicles will probably use rechargeable systems, possibly integrating solar energy collection. Nevertheless, the extended lunar night (lasting about 14 Earth days) and the perpetually dark zones at the poles mean alternative power or energy storage methods are necessary.
Toyota's Lunar Cruiser, for instance, intends to employ a regenerative fuel cell arrangement. This system can create hydrogen via electrolysis using sunlight during the lunar daytime, and then utilize that hydrogen to produce electricity throughout the night. Advanced battery types with high energy storage capacity and broad operational temperature tolerances are also key research areas for JAXA and other space organisations. The energy conservation of all parts, including tyres designed for low rolling friction, is critically important.
Exploring the Unknown Lunar South Pole
The Moon's southern polar region, the destination for forthcoming Artemis expeditions, is an area of striking differences. It features craters in permanent shadow that might contain water ice, alongside areas experiencing almost continuous sunlight. Travelling across this landscape will be demanding. The low angle of the sun casts long, rapidly shifting shadows that can hide dangers. Rovers will need advanced guidance systems, potentially with autonomous driving functions, to move safely through this intricate environment.
Nasa's VIPER rover, a robotic mission about the size of a golf cart designed to look for water ice, will provide crucial information about operating in this area. The LTV will use these findings, incorporating cutting-edge communication and navigation technology. The capacity to drive independently or be guided remotely from Earth or the Lunar Gateway is a vital prerequisite for optimising scientific output and maintaining operational adaptability.
Prioritising Astronaut Well-being on Long Treks
For expeditions involving human crews, the well-being of astronauts is paramount. The LTV will permit astronauts to journey much greater distances from their lander or habitat than previously possible, potentially for several days continuously. This increased travel capacity means the rover must be extraordinarily dependable. Backup systems, strong life-support connections, and efficient radiation protection will be essential. The tyres are a critical component in this safety framework. A tyre malfunction far from a base could place the crew in considerable jeopardy.
The engineering of the LTV also needs to account for how easily astronauts in cumbersome spacesuits can enter and exit, and its ability to manage emergency situations. Creating such vehicles frequently includes thorough human factors assessments to confirm that all systems are not merely operational but also usable by astronauts performing tasks in the difficult lunar setting.
The Significance of Robotics and Preliminary Missions
Robotic undertakings frequently act as forerunners to human exploration. They scout potential locations, assess new technologies, and define the characteristics of the environment. Expeditions like VIPER will collect essential data regarding the whereabouts and ease of access to lunar resources, such as water ice. This knowledge is crucial for organising future human missions and choosing landing spots for the Artemis initiative. These robotic explorers also evaluate key systems, including movement and tyre effectiveness, within the actual lunar conditions.
The LTV itself will possess robotic functions, enabling it to function autonomously or be managed by remote control when astronauts are not on the Moon. This feature facilitates ongoing scientific work and resource investigation during the periods between crewed missions, thereby maximising the usefulness of this important asset. This cooperative relationship between robotic and human exploration forms a fundamental part of the Artemis approach.
Earthly Benefits: From Lunar Tyres to Terrestrial Uses
The concentrated research and development efforts for creating tyres suitable for space missions often lead to significant technological breakthroughs that find uses back on our planet. The Smart Tire Company’s creation of nitinol bicycle and motorcycle tyres is a direct outcome of Nasa-supported investigation into super-elastic substances for Martian rovers. These air-free, highly resilient tyres could provide substantial advantages for consumers looking for options that require no maintenance and are immune to punctures.
Likewise, advancements in composite substances, air-free tyre designs, and sophisticated production methods developed by firms such as Michelin and Bridgestone for lunar use could be adapted for earth-based automotive, aerospace, or industrial applications. Goodyear, another enterprise with a background in creating non-pneumatic tyres, including those for the Apollo lunar roving vehicle, has also investigated air-free tyres for uses like commercial grass-cutting machines. This movement of technology illustrates the wider economic and societal gains from investing in space exploration.
Cultivating a Lasting Lunar Economy
The far-reaching plan for lunar exploration encompasses the establishment of an enduring human settlement, which could potentially foster the growth of a lunar-based economy. This might entail using lunar materials (In-Situ Resource Utilisation - ISRU), like water ice for life support and as rocket propellant, or minerals for building purposes. Trustworthy and effective rovers, fitted with sophisticated tyres, are vital for finding, gathering, and moving these resources.
The Artemis Accords, which outline principles for peaceful and cooperative lunar activities, establish a basis for international and commercial collaborations in these upcoming ventures. As operations on the Moon increase, the need for dependable surface transport will also rise. This could generate business prospects for companies involved in creating and running lunar vehicles and their essential parts, including the critically important tyres.
Global Partnership: A Unified Advance to the Moon
The Artemis initiative is distinguished by its strong focus on worldwide cooperation. Many nations and space organisations, such as the ESA, the Canadian Space Agency (CSA), and the Japan Aerospace Exploration Agency (JAXA), are providing equipment, knowledge, and astronauts for these missions. This global teamwork combines resources and understanding, quickening the progress of lunar discovery.
Canada, for example, supplies the Canadarm3 robotic manipulator for the Lunar Gateway station. ESA contributes the European Service Module for the Orion vessel and the ESPRIT module for refuelling and communications to Gateway. Japan participates in creating a pressurised rover and other systems. This spirit of collaboration also applies to the creation of surface infrastructure, where global partners might assist with or use the LTV and its innovative tyre system. The Artemis Accords seek to guarantee these joint efforts proceed with safety and openness.
The Horizon: Habitats and Extended Stays on the Moon
Ultimately, the objective of initiatives like Artemis is to facilitate prolonged human habitation on the Moon, possibly within permanent or semi-permanent dwellings. Nasa plans for an Artemis Base Camp situated at the Moon's southern pole. This facility would feature a surface dwelling, power generation systems, and transport platforms such as the LTV. Such a base would permit astronauts to reside and perform duties on the Moon for several months at a stretch, carrying out detailed scientific studies and evaluating systems for eventual journeys to Mars.
Creating these habitats, some possibly employing inflatable structures or 3D-printed components made from lunar regolith, presents a formidable engineering task. Dependable rovers equipped with robust tyres will be crucial for building, maintaining, and exploring from these prospective lunar settlements, truly helping humanity to become a species inhabiting multiple planets, one revolution of an advanced wheel at a time.
Recently Added
Categories
- Arts And Humanities
- Blog
- Business And Management
- Criminology
- Education
- Environment And Conservation
- Farming And Animal Care
- Geopolitics
- Lifestyle And Beauty
- Medicine And Science
- Mental Health
- Nutrition And Diet
- Religion And Spirituality
- Social Care And Health
- Sport And Fitness
- Technology
- Uncategorized
- Videos