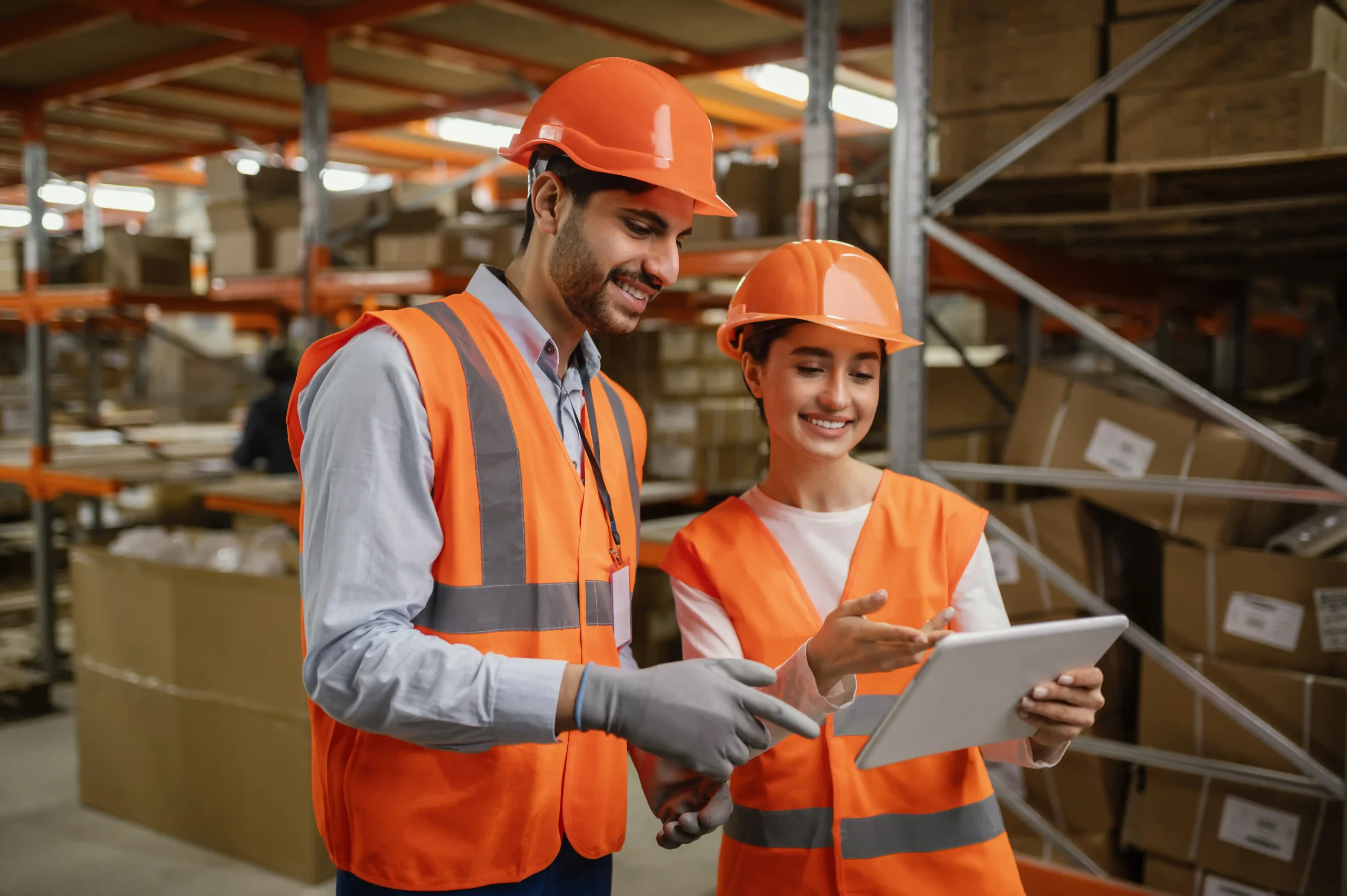
Workplace Safety Breach Costs Firm
Workplace Safety Breach: Engineering Firm Fined Following Serious Injury
A County Tyrone-based engineering company, Caledon Precision Engineering Limited, has found itself facing a substantial £25,000 fine. This comes after a Craigavon Crown Court hearing, where the company pleaded guilty to a health and safety violation. The charges stem from a severe workplace incident on October 10, 2022, in which an employee suffered serious hand injuries.
The Incident
During routine operations, the worker was using emery cloth on an automatic lathe for the purpose of rust removal from a metal component. However, investigations revealed a critical lapse in safety protocols – the interlocking doors of the lathe had been bypassed, enabling it to operate even while open.
HSENI Condemns Company's Negligence
HSENI Inspector Gavin Rowan offered his strong condemnation of the situation. He emphasized that employers have a clear legal responsibility to protect employees and any bystanders from potential harm caused by unguarded machinery.
"Incidents like these, involving emery cloth and metalworking lathes, are sadly not uncommon," Rowan stated. "The consequences are often devastating, including broken bones, dislocations, and tragically, amputations."
Safety Standards Violated
Furthermore, Rowan made it clear that applying emery cloth by hand to a rotating lathe, whether manual or automatic, is strictly prohibited. To allow such actions constitutes a severe breach of established workplace safety practices.
Let's Talk About Emery Cloth
For those unfamiliar, emery cloth is an abrasive akin to sandpaper. It's frequently used for polishing, sizing, or deburring metal components secured within a lathe's rotating chuck. However, direct hand application of emery cloth while the lathe is in operation is inherently dangerous.
Alternatives for Safe Metal Finishing
Thankfully, several alternative and far safer methods exist for finishing metal components held in a lathe. Such techniques include:
Mounted points and flap wheels: Abrasive tools specifically designed for attachment to power tools can be used within a lathe. These tools provide controlled surface finishing without the inherent risks of applying materials by hand.
Parting-off tools: These special lathe tools remove surface material in a controlled manner during the shaping and sizing of metal components.
External grinding machines: Designed for the express purpose of precision grinding, these offer superior control and safety when finishing metal parts.
Protective Guards: Critical Safety Components
It's important to understand the function of protective guards on machinery like lathes. They provide a physical barrier between the operator and the moving parts of the machine. This safeguarding is absolutely essential to prevent entanglement or crushing accidents. Lathe guards may come in various forms:
Interlocking guards: These guards are electrically connected to the machine's power supply. The lathe will not function unless these guards are securely closed at all times.
Fixed guards: Rigidly attached to the machine's frame, these offer a permanent barrier. However, they may require removal during maintenance or tool changes.
Adjustable guards: These provide protection while still offering operational flexibility.
The Importance of Regular Maintenance and Inspection
Alongside appropriate guarding, proactive maintenance and inspections of machinery are paramount. Employers have a duty to ensure regular checks of all safety features, including guards. Any defects or compromises should be immediately rectified, and the operation of such machinery prohibited until repairs are complete.
Training for Operators: A Must
Moreover, comprehensive training for all machine operators is a cornerstone of workplace safety. Employees must understand the correct and safe use of equipment, the risks inherent to their jobs, and the critical importance of maintaining all safety devices. Training should not be a one-time event but refreshed through regular updates and assessments.
Consequences of Safety Failures
As this case with Caledon Precision Engineering Limited demonstrates, failing to prioritize safety has serious repercussions. Beyond the devastating impact on any injured employees, companies face substantial fines, reputational damage, and potential legal liabilities.
The Essential Role of a Safety-First Culture
While regulations, guarding, and training are crucial, they're just one aspect of workplace safety. Cultivating a genuine safety culture throughout a company is vital. In such a culture:
Safety is the top priority: From management to the newest employee, everyone fully understands that safety takes precedence over deadlines, costs, or any other factor.
Open communication is encouraged: Workers feel empowered to report safety concerns, near-misses, and any unsafe practices without fearing repercussions.
Near-misses are opportunities: Incidents and near misses are not brushed aside, but thoroughly investigated. This allows for the identification of systemic problems and the implementation of solutions to prevent recurrences.
Accountability is shared: Responsibility for safety isn't simply on the shoulders of workers. Managers, supervisors, and even company directors have a role in demonstrating safety leadership and holding everyone accountable for safety standards.
Proactive Steps for Employers
Employers can take several specific actions to foster a strong safety culture in their workplaces:
Conduct regular risk assessments: Proactively identify and address potential hazards within the work environment. This should be a continuous process.
Invest in safety equipment and resources: Provide workers with all appropriate safety gear, ensure that guarding is correctly maintained, and allocate dedicated budgets for safety upgrades and initiatives.
Employee involvement: Worker participation in safety discussions, hazard identification, and solution development is essential.
Recognition and rewards: Celebrate achievements in safety milestones. This reinforces positive behaviors and a commitment to safety excellence.
Responsibilities of Employees
Similarly, employees have an equally important role in maintaining safe working practices:
Follow safe procedures: Never cut corners or bypass safety protocols, even under time pressure.
Utilize provided safety equipment: Wear personal protective equipment correctly and consistently.
Speak up: Never hesitate to report any potential dangers or unsafe conditions to supervisors.
Participate in training: Engage actively with training programs and safety initiatives offered by the employer.
The Wider Impact of Workplace Accidents
It's vital to recognize that workplace accidents cause ripples beyond the immediate workplace. Injured employees face physical pain, emotional distress, and potential long-term disabilities. Families experience worry, financial hardship, and the disruption of losing a loved one's primary or secondary income stream.
Furthermore, employers face lost productivity, the costs of replacing injured workers, higher insurance premiums, and the erosion of overall company morale when safety isn't valued.
Safety Support and Resources are Available
Companies need to realize they aren't alone in the effort to build a safety-focused workplace. A wealth of valuable resources is available from various organizations:
The Health and Safety Executive for Northern Ireland (HSENI): The HSENI offers a wide range of guidance materials on specific industries, hazards, and safety practices. Employers can find sector-relevant guidelines, case studies, and practical advice on risk management through their extensive online resources.
Trade Unions: Trade unions play a vital role in advocating for workers' health and safety. They can provide invaluable support to employees in understanding their rights, reporting safety concerns, and participating in workplace health and safety committees.
Industry Organizations: Many industry sectors have dedicated associations that provide safety-specific guidance and best practices. These organizations frequently offer training programs, seminars, and networking opportunities for knowledge sharing centered on workplace safety.
Safety Consultants: Specialized safety consultants can provide tailored assessments of a workplace, identify potential hazards, and offer recommendations to improve safety procedures and compliance with regulations.
Prevention: The Ultimate Goal
While accidents regrettably happen, the best outcome is preventing them before they occur. Employers must shift their mindset away from a reactive stance towards one that is proactive in managing safety risks. Here are some critical steps for prevention-focused safety management:
Prioritize regular safety inspections and audits: Going beyond basic compliance, conduct proactive workplace walkthroughs with an eye for potential hazards.
Encourage a blame-free reporting culture: Create an environment where workers feel comfortable reporting safety issues without fear of negative consequences.
Invest in continuous improvement: View safety as a journey of ongoing improvement, allocating resources towards upgrading systems, training, and equipment as needed.
Emphasize prevention in performance reviews: Hold managers and supervisors accountable for safety outcomes within their areas of responsibility.
The Path to a Safer Workplace
The incident at Caledon Precision Engineering Limited serves as a stark reminder of the importance of workplace safety. Employers and workers alike have a shared duty to create workplaces where employees can return home safe and healthy at the end of each workday.
By taking proactive steps, fostering a safety-driven culture, and utilizing the support of available resources, companies can move closer to preventing injuries and building a workplace where safety genuinely comes first.
The Long-Lasting Consequences of Safety Lapses
It's important to understand that the repercussions of a workplace injury can extend far beyond immediate medical attention and fines. Workers who sustain serious injuries may face life-altering repercussions, such as:
Permanent Disability: Severe injuries can lead to impairments that permanently limit a person's ability to work or perform everyday tasks.
Chronic pain and suffering: Injuries may lead to persistent pain and discomfort, significantly impacting a person's quality of life.
Psychological trauma: Workplace accidents often leave emotional scars, with victims potentially experiencing anxiety, depression, or post-traumatic stress disorder (PTSD).
Loss of livelihood: In cases of disabling injuries, workers may be unable to return to their previous jobs. This can result in substantial financial hardship and uncertainty about their future.
The Toll on Families and Communities
Moreover, the impact extends to families and communities. When a breadwinner is unable to work due to a workplace injury, financial strain and emotional burdens can ripple outward. Children may face limited opportunities due to lost income, and spouses are often forced into the role of both income provider and caretaker. Even broader communities may feel the effects, particularly in towns with a single major employer.
It's Never 'Just an Accident'
A critical point must be remembered: workplace injuries and fatalities are rarely merely misfortunes. They are often the result of preventable failures. Employers must see the consequences beyond the immediate fines and focus on the potential human cost of lax safety protocols.
The Call for Constant Vigilance
While the outcome in the case of Caledon Precision Engineering Limited sends a strong message, it's crucial that companies don't become complacent in the wake of such a case. Safety must be a continuous endeavor built on these key principles:
Safety is a choice: It's not a matter of luck, but the result of conscious planning, investment, and a commitment to following established procedures.
Complacency is a risk: Even workplaces with strong safety records need constant review and improvement to prevent the erosion of standards over time.
Leadership sets the tone: Safety must be driven by management, with clear accountability and communication throughout the company.
Conclusion
Workplace safety is a matter of both legal compliance and moral imperative. Employers have a responsibility to do everything within their power to ensure a safe environment for their workers. By investing in safety, fostering a culture of shared responsibility, and utilizing available resources, preventable injuries and the devastating consequences that follow can be avoided.
Companies must understand that a safe workplace is not just a regulatory checkbox; it's fundamental to the well-being of their employees, their families, and the wider community they serve.
Recently Added
Categories
- Abnormal psychology
- Acupuncture
- Air Cabin Crew
- Aircrafts And Aerospace
- Anatomy And Physiology
- Animal Care
- animal communication
- Anthropology
- Anxiety management
- Aromatherapy
- Art Therapy
- Artificial Intelligence
- Arts And Humanities
- Autism
- Beauty Therapy
- Birth Doula
- Blog
- Body Language
- Borderline Personality Disorder
- Brand Building
- British Politics
- Business and Accounting
- Business Law
- Child Psychology
- Classic Vehicle Restoration
- Classroom Behavior Management
- Cognitive Behavioral Therapy
- Complementary Health
- Confidence Building
- Conflict Resolution
- Consumer Behaviour
- Counselling And Psychology
- Couples Therapy
- Craniosacral Therapy
- Criminology
- decision making
- Decontamination And Sterile Services
- Dementia
- Dental Practice
- Detox
- Diabetes
- Digital Forensics
- Digital Photography
- distance education
- Dog Training
- Dream Analysis
- Ear Candling
- Economics
- Educational Psychology
- Egyptology
- Elearning
- Emotional Freedom Technique
- English Literature
- Environment And Conservation
- Ethical Hacking
- Feature Writing
- Filmmaking
- Florist
- Forensic Science And Profiling
- Fundraising
- Gaming
- Gardening And Horticulture
- Gemmology
- Genealogy
- Genetics
- Gestalt Therapy
- Grief Counselling
- Health And Safety
- Health And Therapies
- Healthy ageing
- Heraldry
- Hobbies And Lifestyle
- Homeopathy
- Human Resource
- Hypnotherapy
- Interrogations And Confessions Psychology
- Library And Information Science
- Life Coach
- Management
- Maritime Law And Shipping Contracts
- Medical Secretary
- Medicine And Science
- Mental Health
- Microbiology
- mind mapping
- Motorsport Engineering
- Mushroom Growing
- Nail Technician
- Negotiation Skills
- Novel Writing
- Numerology
- Nutrition And Diet
- Pain Management
- Palmistry
- pilates
- Property investment
- Quality Control and Assurance
- Reiki
- Relationship Psychology
- Restorative Justice
- Safeguarding
- Schizophrenia
- Social Care
- sports nutrition
- Sports Psychology
- Success Stories
- Teaching Assistant
- Time Management
- Uncategorized
- Universe And Space
- Vexillology
- Videos
- Wedding Planner and Events Management
- Wind Power
- Wines
- Yoga